РЕКОМЕНДАЦИИ
по работе на индукционной вакуумно-компрессионной литейной установке
УЛВК-10МК.
Н.
А. Швыргун. Главный конструктор проекта ООО "СПАРК-ДОН, ЛТД"
|
|
|
|
|
|
Статья
на google.com |
 |
|
|
|
|
|
|
|
|
|
|
|
|
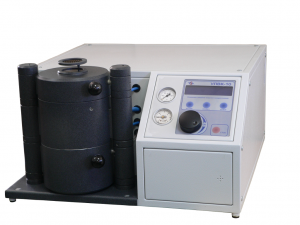 |
|
|
Вакуумная
литейная установка УЛВК-10МК относится к классу установок, работающих
по принципу плавки и литья в вакууме с последующим прессованием
избыточным давлением. К этому классу относятся также литейные установки
"Nautilus T" фирмы Bego, "Heracast IQ" фирмы
Heraeus Kulzer, "Induret Compact" фирмы Reitel.
Отличия
в работе всех этих установок заключаются в принципе заливки расплава
в литейную полость и разных типах используемого тигля.
Рекомендации
по плавке стоматологических сплавов и конструированию литниковой
системы являются общими для любой установки данного класса.
|
|
|
РАЗМЕЩЕНИЕ, УСТАНОВКА
И ПОДКЛЮЧЕНИЕ К СЕТЯМ ЭЛЕКТРОЭНЕРГИИ, ВОЗДУХА И ВОДЫ.
1.
Установка должна быть размещена на столе с твердой, нескользящей
поверхностью, площадью не менее 70,0 х 60,0 см (глубина, ширина),
так, чтобы было обеспечено её горизонтальное расположение.
Входные и выходные штуцеры для воды и воздуха, расположенные на
задней стенке, не должны быть закрыты и заблокированы. Минимальное
расстояние до стены 100 мм. Нельзя располагать что-либо в зоне открытия
крышки камеры индуктора и камеры опоки.
2.
Установка подключается к электросети 220 ±22 вольт , 50Гц с
помощью вилки европейского стандарта, имеющей заземляющий контакт.
На распределительном щитке должен быть установлен автоматический
выключатель, рассчитанный на ток 25 А, через который подключается
установка. Фаза, на которую подключена установка, не должна нагружаться
другими потребителями, например, муфельными печами.
3.
Установка подключается к источнику сжатого воздуха давлением
7,0-8,0 бар (0,7 – 0,8 МПа). Сжатый воздух должен быть чистым и
сухим. В случае влажного воздуха необходимо установить гидросепаратор-фильтр.
Минимальный внутренний диаметр шланга для подвода сжатого воздуха
- 10 мм. Источник сжатого воздуха должен быть производительностью
не менее 180 литров в минуту. Рекомендуется использовать отдельный
ресивер сжатого воздуха объемом 20-30 литров, установленный в непосредственной
близости к установке.
При
использовании в качестве агента для прессования аргона, баллон с
аргоном и установленным на нём редуктором должен быть соединён с
установкой шлангом минимально возможной длины диаметром 10мм.
4.
Подключение установки к источнику охлаждающей жидкости (вода) может
быть выполнено двумя способами.
 4.а
Охлаждение установки от водопроводной сети.
Входной
штуцер установки по воде необходимо соединить шлангом внутреннего
диаметра 5 мм с источником воды, а шланг с выходного штуцера опустить
в раковину. Давление воды должно быть около 1,5 бар, при этом расход
воды должен быть не менее 2-х литров в минуту. Проверить это можно,
заполняя мерную емкость из шланга с выходного штуцера.
Данный
вариант подключения воды нежелателен, так как приводитк отложению
солей внутри индуктора и сокращает срок его службы.
 4.б
Рекомендуемый вариант водяного охлаждения установки - от модуля
водяного охлаждения МАВО-1М.
Для этого необходимо подсоединить модуль к установке согласно «Руководства
по эксплуатации». Шланги для подсоединения прилагаются.
Бак
модуля заполняется дистиллированной водой, использование которой
исключает отложение солей. |
|
|
|
|
|
|
|
|
|
|
|
|
|
|
|
|
|
|
|
|
|
|
|
|
|
|
|
|
|
ПОДГОТОВКА К РАБОТЕ. |
|
|
Перед
включением установки в сеть и работой с ней внимательно изучите
«Руководство по эксплуатации» СП0076.00.00.000.РЭ.
Подключите
установку к однофазной электрической сети переменного тока 220В,
50Гц.
Электрическая
сеть не должна нагружаться другими пользователями.
Подайте
на установку сжатый воздух, при этом манометр установки "ДАВЛЕНИЕ"
должен показать 6 ± 0,5бар (0,6 ± 0,05 Мпа).
Откройте литейную камеру и установите теплоизоляционный вкладыш,
а затем — центрирующий вкладыш с отверстием, соответствующим диаметру
выбранной опоки.
Допускается
использование опок:
1. С вкладышем: стандартных типоразмеров 1Х, 3Х, 6Х, 9Х (диаметр
35-80 мм, высота - 55 мм);
2. Без вкладыша: нестандартных размеров, высотой не более 55 мм
и диаметром до 100 мм.
|
|
|
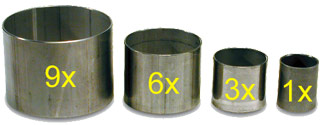 |
Опочные кольца
круглые металлические типоразмеров 1Х, 3Х, 6Х, 9Х. |
|
|
|
|
|
|
|
|
|
|
|
|
|
|
|
|
|
|
|
|
|
|
|
|
|
|
|
|
|
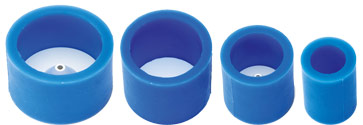
|
Опочные кольца
круглые силиконовые типоразмеров 1Х, 3Х, 6Х, 9Х. |
|
|
Откройте
крышку камеры индуктора и с помощью пинцета установите в затвор
керамическую вставку. |
|
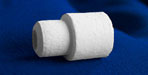 |
Вставка должны быть без трещин и сколов. Поверхность вставки, которой
она соприкасается с тиглем, должна быть гладкой. Если на ней остался
шлак или металл, уберите их шлифовальной алмазной головкой.
|
|
|
РАБОТА. |
|
|
Откройте
крышку камеры индуктора и установите тигель в отверстие держателя.
|
|
|
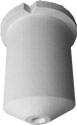 |
В установке УЛВК-10МК применяются тигли типа «Induret" с
донным разливом расплава.
Никогда не используйте один и тот же тигель для плавки сплавов различного
типа. При многократном использовании одного и того же тигля
для плавки различных сплавов возникает опасность того, что оставшиеся
от предыдущих сплавов частички растворятся в новом сплаве и повлияют
на его качество. |
|
|
Регулировочной
ручкой отрегулируйте положение керамической вставки затвора относительно
тигля.
Загрузите
тигель металлом. При этом необходимо располагать кусочки металла
ближе к стенкам тигля, что обеспечит оптимальные условия для процесса
плавления.
|
|
|
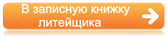 |
Исходя
из того факта, что вихревые токи, вызывающие нагрев заготовки, протекают
по её периметру, следует важный практический вывод:
Для
увеличения эффективности нагрева и сокращения времени плавки следует
использовать тот сплав, который при одинаковых физико-химических
свойствах, имеет меньший диаметр единичной заготовки.
При
увеличении количества заготовок сплава, одновременно загруженных
в тигель, сумма их длин окружностей увеличивается. Следовательно,
при постоянной глубине горячего проникновения тока, объем, в котором
выделяется мощность, увеличивается. Соответственно, металл будет
нагрет до необходимой температуры быстрее.
Идеальными
условиями для проведения плавки будет следующий состав загрузки:
50...70% "первичного металла" в виде цилиндров с диаметром
6...10мм и 30...50% "вторичного металла" в виде элементов
литниковой системы диаметром 3...5мм.
|
|
|
|
|
|
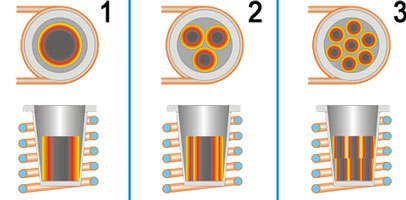
|
|
|
|
|
1.
- загрузка в виде единичной заготовки диаметром D=20мм. Эффективность
нагрева неудовлетворительная. Время плавки максимальное.
2. - загрузка в виде нескольких заготовок диаметром D=12мм.
Эффективность нагрева удовлетворительная.
3. - загрузка в виде нескольких заготовок диаметром D=8мм.
Эффективность нагрева высокая. Время плавки минимальное. |
|
Закройте
крышку камеры индуктора и камеру опоки. Включите выключатель "СЕТЬ".
При этом прозвучит звуковой сигнал, и на дисплее появятся надписи: |
|
|
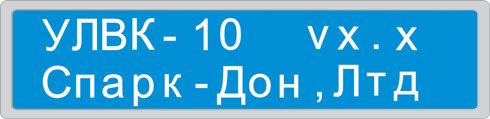 |
|
|
|
|
|
|
|
|
|
|
|
|
|
где vх.х - версия
программного обеспечения. Через 1...2 с. на дисплее появится надпись,
предлагающая Вам включить подачу водяного охлаждения в установку. |
|
|
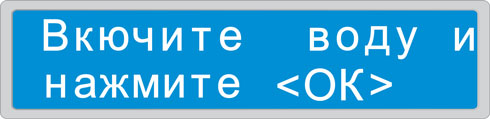 |
|
|
Включите
подачу воды в систему охлаждения установки и, после паузы в 3...5
секунд, нажмите ручку многофункционального регулятора (задатчика).
Вода должна быть подана в систему охлаждения только после
появления этой надписи, что необходимо для диагностики датчика потока
воды в системе.
На
дисплее появится следующая информация: |
|
|
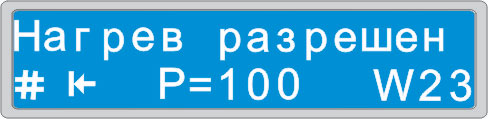 |
|
|
 Установите
параметры плавки и литья.
 На
установке регулируются три параметра: мощность генератора P (в
процентах), время литья t1 (промежуток между открытием затвора
и подачей сжатого воздуха в плавильно-литейный блок, в секундах)
и время прессования t2 (в секундах).
 Регулирование
параметра выполняется следующим образом: нажатием задатчика осуществляется
переход между параметрами процесса:
 P
- заданная мощность нагрева (в процентах),
 t1
- время литья (в секундах),
 t2
- время прессования (в секундах).
 Вращением
задатчика устанавливается требуемая величина регулируемого параметра.
 При
включении установки выбран параметр «P».
Мощность
"P" регулируется в пределах от 20 до 100%, время литья
"t1" — от 0.25 до 5 секунд, время прессования "t2"
– от 0 до 60 секунд. Дискретность регулирования: 2%, 0.25 секунды
и 1 секунда соответственно. Первоначально мощность генератора
установлена на 100%, время литья — 1 секунда, а время прессования
– 60 секунд.
После первого проведенного процесса литья, внесенные в параметры
изменения сохраняются в энергонезависимой памяти.
 Вращая
ручку многофункционального регулятора (задатчика), установите
уровень заданной мощности равный 85%. При этом дисплей примет
следующий вид:
|
|
|
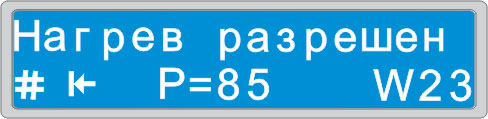 |
|
|
Для
задания времени литья "t1" нажмите на ручку многофункционального
регулятора (задатчика). При этом на месте индикации уровня заданной
мощности "P" появится значение времени литья "t1".
Вращая ручку задатчика, установите нужное значение t1.
|
|
|
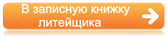 |
Выбор
значения времени литья "t1" определяется количеством сплава,
которое Вы собираетесь плавить. Количество необходимого для работы
сплава определяется как произведение массы восковой композиции и
плотности используемого сплава. Например, при весе восковой композиции
9г и плотности используемого сплава 8,2 г/см3, для выполнения литья
необходимо и достаточно 73г сплава. В этом случае необходимо установить
значение времени литья t1=0,75с.
Для
установки УЛВК-10МК, с учетом размеров тигля (высота, диаметр, конусность)
и размеров его выпускного отверстия (оптимально-6,5мм), при использовании
«усредненного стоматологического сплава» можно руководствоваться
следующим соотношением. Истечение 25г сплава происходит за время
0,25с. Соответственно, 50г расплава полностью вытекут за 0,5с, 75г-за
0,75с.
Эти
ориентировочные значения времени литья должны быть уточнены литейщиком
путем проведения опытной плавки с конкретным типом сплава.
В
вакуумных литейных установках, работающих по принципу "плавка
и литьё в вакууме с последующим прессованием избыточным давлением"
расчёт необходимого количество сплава отличается
от аналогичного расчёта при работе на центробежных индукционных
литейных (например, ЦЕНТРОЛИТ-70М). При работе на центробежных установках
к расчётному количеству сплава необходимо прибавлять 10...15г сплава
для заполнения конуса. В случае с вакуумными литейными установками
этого делать не надо. В противном случае, это отрицательно повлияет
на качество литья.
|
|
|
|
|
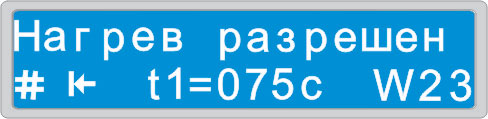 |
|
|
Проконтролируйте
значение заданного времени прессования "t2". При необходимости,
установите новое его значение. Мы рекомендуем работать при времени
прессования t2=60c.
|
|
|
Стадия
№1. Предварительный нагрев.
Положение
керамической вставки затвора относительно тигля отрегулировано.
Тигель загружен металлом. Параметры плавки и литья установлены.
Установка готова к процессу плавки металла (фаза №1).
|
|
|
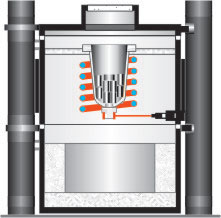 |
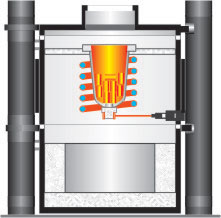 |
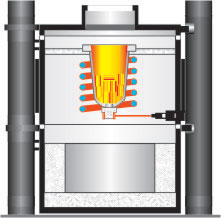 |
|
|
Фаза
№1 |
Фаза №2 |
Фаза №3 |
|
|
Процесс
предварительной плавки металла можно проводить в двух режимах,
обеспечивающих универсальность и удобство при эксплуатации установки:
Режим
1. Плавка с предварительным нагревом в воздушной среде.
Нажмите
кнопку «НАГРЕВ». Включится генератор и начнется процесс
нагрева (фаза №2). На дисплее установки отображается наименование
стадии работы ("Нагрев"), а также величина задания
уровня мощности генератора (в процентах), реальная текущая мощность
генератора, температура воды в системе охлаждения, состояние датчиков
закрытия камеры индуктора и камеры опоки, время от начала процесса,
положение керамической вставки затвора относительно выходного
отверстия тигля.
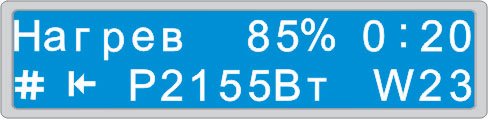
Через
смотровое окно со светофильтром наблюдайте за состоянием металла.
Продолжайте нагрев до того момента, когда металл начнет ярко светиться
(фаза №3). Перед тем, как приступить к загрузке опоки в
камеру, рекомендуется уменьшить мощность генератора приблизительно
в два раза, ориентируясь по показаниям в нижней строке дисплея,
во избежание преждевременного разжижения металла. Камера индуктора
и камера опоки при работе в этом режиме не герметизируется.
Режим
2. Плавка с предварительным нагревом в вакууме.
Нажмите
кнопку «ПЛАВКА». Включится генератор, камеры опоки и индуктора
герметизируются и начнется откачка воздуха. Крышка камеры индуктора
и камера опоки заблокируются. Стрелка мановакууметра начнет перемещаться
с нуля до –0,7…–0,8 кгс/см2. Начнется процесс нагрева металла
(фаза №2).
На
дисплее установки отображается наименование стадии работы ("Плавка"),
а также, как и в предыдущем случае, величина задания уровня мощности
генератора (в процентах), реальная текущая мощность генератора,
температура воды в системе охлаждения, состояние датчиков закрытия
камеры индуктора и камеры опоки, время от начала процесса, положение
керамической вставки затвора относительно тигля.
Процесс
нагрева можно отслеживать через смотровое окно со светофильтром.
Когда металл прогреется и начнет ярко светиться (фаза №3)
нажмите кнопку «СТОП». Генератор отключится и начнется
стравливание воздуха из камер и уплотнительных колец. Крышка камеры
индуктора и камера опоки разблокируются.
Стадия
№1 (предварительный нагрев) окончена.
Никогда не доводите металл в процессе предварительного нагрева
до состояния, когда он начнёт плавиться. В противном случае это
может в дальнейшем привести к ухудшению условий плавки.
Индицируемая на дисплее мощность в данном описании показана условно.
Реальное её значение, отображаемое на индикаторе, будет зависеть
от конкретных условий плавки: тип сплава, его количество и геометрические
размеры единицы сплава; особенности расположения сплава в тигле
и т.д.
С целью сокращения времени перехода от предварительного нагрева
металла к его плавке и литью мы рекомендуем работать без вакууммирования
литейных камер во время предварительного нагрева металла (Режим
№1).
|
|
|
Стадия
№2. Плавка металла в вакууме. |
|
|
Откройте
камеру опоки и установите предварительно нагретую опоку в отверстие
вкладыша, воспользовавшись специальными щипцами (фаза №4).
Если используется нестандартная опока, то ее надо установить так,
чтобы литниковое отверстие опоки совпало с перекрестием, нанесенным
на теплоизоляции. Время для загрузки опоки в литейную камеру не
должно превышать 10-15 секунд, чтобы не допустить существенного
охлаждения металла и литейной формы.
После
загрузки опоки, закройте камеру опоки до упора и нажмите кнопку
«ПЛАВКА».
Камеры индуктора и опоки автоматически герметизируются. Крышка камеры
индуктора и камера опоки заблокируются. Из литейных камер начнется
откачка воздуха. При этом стрелка мановакууметра начнет перемещаться
с нуля до –0,7…–0,8 кгс/см2. Одновременно включится генератор и
начнется процесс плавки металла (фаза №5). |
|
|
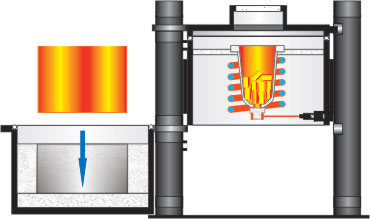 |
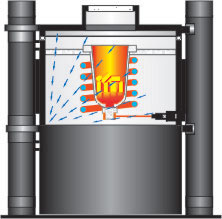 |
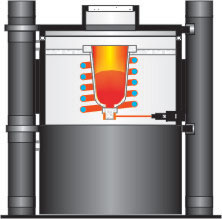 |
|
|
Фаза
№4 |
Фаза №5 |
Фаза №6 |
|
|
На
дисплее установки отображается наименование стадии работы ("Плавка"),
а также величина задания уровня мощности генератора (в процентах),
реальная текущая мощность генератора, температура воды в системе
охлаждения, состояние датчиков закрытия камеры индуктора и камеры
опоки, время от начала процесса, положение керамической вставки
затвора относительно тигля.
Вы
можете плавно регулировать мощность генератора для получения оптимальных
условий плавки. Начинайте плавку при уровне мощности равном 100%.
После погружения последней твёрдой части в плавильную ванну уменьшите
мощность до 80...85%.
Продолжайте нагрев до полного расплавления металла (фаза №6).
На поверхности расплава образуется тонкая оксидная плёнка. После
появления в ней разрывов дождитесь момента, когда оксидная плёнка
разойдётся по периметру тигля. Зеркало расплава станет гладким и
блестящем. Расплав готов к литью. |
|
|
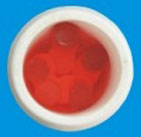 |
|
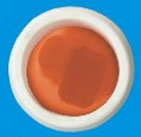 |
|
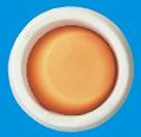 |
|
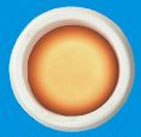 |
|
|
1. Металл
начал размягчаться и оплывать. |
|
2. Отдельные кусочки
металла начали сплавляться вместе. |
|
3. Металл полностью
расплавлен, но видны легкие тени. |
|
4. Поверхность расплава
ярко светится. «Тень» исчезла. Металл готов к литью. |
|
|
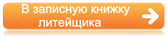 |
В
вакуумных литейных установках, работающих по принципу "плавка
и литьё в вакууме с последующим прессованием избыточным давлением"
в литейных камерах поддерживается не абсолютный вакуум, а разреженная
атмосфера с остаточным давлением 100...150мБар. Смысл уменьшения
мощности до 80...85% на заключительной стадии плавки заключается
в том, чтобы обеспечить минимальный градиент температуры по всему
объёму расплава к моменту достижения температурой расплава значения
температуры литья сплава. Важно отметить, что благодаря использованию
в литейной установке УЛВК-10МК генератора с рабочей частотой 440кГц,
этот процесс протекает при отсутствии разрывов оксидной плёнки,
защищающей расплав от остатков воздуха в камере. Если же проводить
плавку при максимальной мощности установки, оксидная плёнка разорвётся
раньше необходимого, открывая зеркало расплава и делая его доступным
для реакции с остатками воздуха в плавильной камере.
|
|
|
|
|
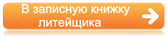 |
Наиболее
важными характеристиками литейных свойств стоматологических сплавов
являются: жидкотекучесть, усадка (линейная и объемная), склонность
к образованию трещин,склонность к поглощению газов и образованию
газовых раковин и пористости в отливках.
Для улучшения жидкотекучести расплава допускается небольшой перегрев
металла, но не выше температуры литья сплава на 75—100°С. Дальнейшее
повышение температуры расплава отрицательно влияет на структуру
металла. Это связано с тем, что растворимость газов в расплаве резко
возрастает при его температуре плавления. Дальнейшее же повышение
температуры расплавленного металла увеличивает растворимость в нем
газа до максимума. Кроме того перегретый расплав, вступая в реакцию
с паковочной массой, способствует дополнительному газообразованию.
В последующем, это приводит к образованию усадочных и газовых раковин,
трещин и пористости.
Если
же расплав при литье имеет низкую температуру, ухудшаются условия
удаления газов из металла и питания отливок во время кристаллизаци,
существенно увеличивается опасность незаполнения полости объекта
литья. Получение качественной отлитки, особенно тонкостенных частей
восковой композиции, становится невозможной.
На
практике, после того как оксидная плёнка разойдётся по периметру
тигля, нагрев продолжают ещё несколько секунд (3 - 10 секунд в зависимости
от типа сплава, рекомендаций фирмы производителя сплава по ведению
плавки и параметров плавки) и выполняют литьё.
В
целом, литейщик должен помнить, что лучший результат будет получен
при минимальной температуре расплава, обеспечивающей получение заданных
характеристик объекта литья.
Важную
роль играет правильно сконструированная литниковая система. Размеры,
конфигурация и взаимное расположение составных её частей должны
обеспечивать быстрое заполнение литейной полости расплавом, хороший
газообмен, достаточную подпитку горячим расплавом объектов литья
и их направленную кристаллизацию.
|
|
|
|
|
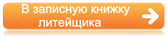 |
Определение
момента заливки зависит от таких факторов как температура плавления
сплава, температура литья сплава, жидкотекучесть сплава - способность
металлического расплава заполнять полость литейной формы. Используйте
рекомендации по ведению плавки, указанные фирмами производителями
сплавов.
Необходимо
учитывать также , что при литье сплавов в вакуумной литейной установке
образуется меньше оксидов и оксидная плёнка тоньше, а, следовательно,
разрывается раньше. |
|
|
|
|
Стадия
№3. Литьё металла в вакууме.
Когда
металл расплавится и будет готов к литью, нажмите кнопку «ЗАТВОР».
При этом откроется затвор и начнется процесс литья (фаза №7...фаза
№9). На дисплее будет отображаться наименование стадии работы
"Литьё" и заданное время литья "t1" с
его обратным отсчётом.
Фаза
№7. При вакуумном литье в литейной полости находится разреженный
воздух. Расплав под воздействием силы тяжести затекает в литейную
полость ламинарным потоком.
Фаза
№8. Нарастающее, по мере затекания расплава, противодействие
сжатого остаточного воздуха способствует равномерному заполнению
расплавом литейной полости. При этом вначале заполняется весь коллектор,
и только после этого расплав заполняет литейную полость каркаса
протеза. В этой фазе давление затекающего расплава уравнивается
с давлением остаточного воздуха в опоке.
Воздух
замешивается в расплав и уходит в направлении заливочной воронки.
Питатель между коллектором и литейной полостью, сам коллектор и
литниковые каналы, идущие к заливочной воронке должны иметь размеры,
способствующие нормальному воздушному обмену.
Противодействие
остаточного воздуха ослабевает. Расплав под воздействием силы тяжести
заполняет каркас протеза, замещая воздух.
Фаза
№9. Остаточный воздух, имеющий давление, превышающее давление
в плавильно-литейном блоке, выходит через литниковый канал в заливочную
воронку (конус) наружу.
При вакуумном литье необходимо брать такое количество сплава,
чтобы расплав после застывания достигал нижнего края заливочной
воронки. В противном случае могут быть проблемы заполнения
литейной полости металлом (непролив), так как выход остаточного
воздуха из опоки будет затруднен. |
|
|
|
|
|
|
|
|
|
|
|
|
|
|
|
|
|
|
|
|
|
|
|
|
|
|
|
|
|
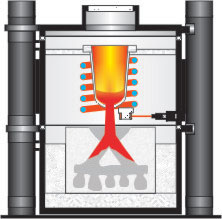 |
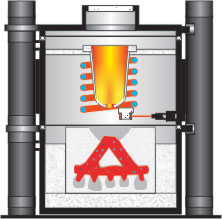 |
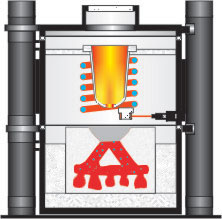 |
|
|
Фаза
№7 |
Фаза №8 |
Фаза №9 |
|
|
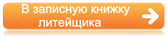 |
При
работе на вакуумных литейных установках, работающих по принципу
плавки и литья в вакууме с последующим прессованием избыточным давлением,
правильное задание времени литья "t1" (т.е. задержки подачи
избыточного давления в плавильно-литейный блок) играет важнейшую
роль в процессе получения качественного литья.
Если
избыточное давление подать в плавильно-литейный блок до того как
расплав под действием силы тяжести заполнит литейную полость, воздух
вместе с расплавом попадёт в литниковые каналы, произойдёт значительное
газонасыщение расплава. Это существенным образом ухудшит условия
воздухообмена между литейной полостью и внешней средой. Газонасыщение
расплава приведёт впоследствии к ярко выраженной внутренней и поверхостной
газовой пористости. Повышается вероятность получения не полностью
пролитых объектов литья.
Если
же избыточное давление подать в плавильно-литейный блок слишком
поздно, не будут созданы условия для эвакуации оставшегося в объекте
литья воздуха и выделяющихся при кристаллизации расплава растворённых
в них газов. Силы тяжести, под действием которой расплав заполняет
опоку, оказывается недостаточно для полноценного питания отливки.
В итоге, отливка будет иметь рыхлую и неоднородную по объёму структуру.
Появятся "непроливы" мелких деталей отливки, на поверхности
отливок будет наблюдаться значительная газовая пористость. .
Для обеспечения требуемой жидкотекучести расплава и обеспечения
хорошего газообмена с целью предупреждения непроливов, газовой пористости,
неконтролируемой усадки продолжительность заполнения опоки не должна
превышать доли секунды, а время подачи избыточного давления в литейные
камеры должно быть максимально синхронизировано с моментом полного
истечения расплава из тигля. |
|
|
Для обеспечения плавного и спокойного (ламинарного) истечения
расплава металла из тигля и равномерного заполнения им литейной
полости опоки необходимо следить за тем, чтобы выходное отверстие
тигля оставалось равным 6,5...7мм.
Уменьшение выходного отвестия тигля до 5мм может привести к слишком
медленному истечению металла из тигля.
Значительное увеличение выходного отверстия тигля приводит к слишком
быстрому истечению расплава, что также не способствует качественному
заполнению литейной полости опоки.
|
|
|
Стадия
№4. Прессование. |
|
|
Фаза
№10.
По
истечении времени литья автоматически включается подача сжатого
воздуха в плавильно-литейный блок. Дисплей установки принимает следующий
вид:
Сжатый
воздух, воздействуя на расплав, обеспечивает сохранение жидкотекучести
металла в литниковых каналах опоки, особенно в наиболее тонких её
сечениях. Расплав вдавливается в литейную форму способствуя заполнению
пустот, в которые он не вошел под действием силы тяжести и вакуума.
Подпрессовка в процессе кристаллизации сплава сжимает газовые включения,
уменьшает усадочную пористость и улучшает структуру металла.
Эффективность
подпрессовки зависит от продолжительности достижения максимального
значения давления в процессе кристаллизации сплава. Чем меньше это
время, тем выше её эффект. Прилагаемая сила давления для уплотнения
сплава составляет 3,5 бара и действует до 60 секунд.
Время
прессования "t2" задается литейщиком и индицируется
на дисплее в виде обратного отсчёта во время стадии прессования.
|
|
|
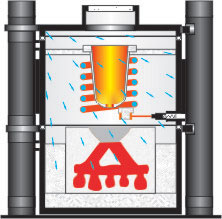
|
 |
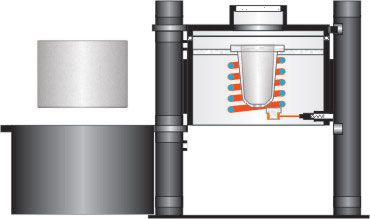 |
|
|
Фаза
№10 |
Фаза №11 |
Фаза №12 |
|
|
По
завершении стадии прессования автоматически включится стравливание
воздуха из камер и уплотнительных колец, крышка камеры индуктора
и камера опоки разблокируются (фаза №11).
На
дисплее установки появляется надпись:
По
окончанию плавки откройте камеру опоки и выньте опоку (фаза №12).
Откройте крышку камеры индуктора и выньте тигель. Если отверстие
на дне тигля загрязнено шлаками и остатками металла, его необходимо
очистить либо заменить тигель новым.
Диаметр отверстия на дне тигля должен быть 6,5 – 7мм. Осмотрите
керамическую вставку на предмет расплавленных участков или загрязнения
шлаками. Если таковые имеются, и поверхность вставки стала неровной,
отшлифуйте ее рабочую поверхность или замените на новую.
Осмотрите
уплотнительные кольца, в случае необходимости протрите их.
Установка
готова к следующему литью.
|
|
|
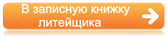 |
При
работе на вакуумных литейных установках, в отличие от литейных установок
с центробежным разливом металла, необходимо брать такое количество
металла, чтобы расплав после застывания достигал нижнего края воронки
опоки. Таким образом, не только экономится дорогостоящий металл,
но и обеспечиваются условия для получения качественной отливки. |
|
|
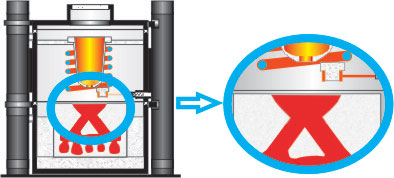 |
|
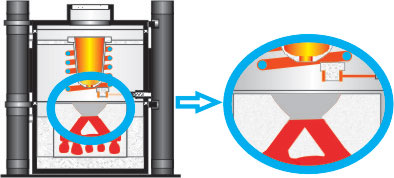 |
|
Расплав после застывания
полностью заполнил воронку опоки. Условия получения качественного
литья не выполнены.
|
|
|
|
|
Расплав после застывания
достиг нижнего края воронки опоки. Условия получения качественного
литья выполнены.
|
|
|
|
|
|
|
|
|
|
|
|
|
|
|
|
|
|
|
|
|
|
|
|
|
|
|
|
|
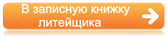 |
ДЕФЕКТЫ
ОТЛИВОК. ПРИЧИНЫ ИХ ВОЗНИКНОВЕНИЯ И СПОСОБЫ. |
|
|
1. Модель залита металлом не полностью.
- Расплав
при литье имеет низкую температуру, не обеспечивающую его достаточную
жидкотекучесть;
Не выполняйте литьё
до того как оксидная плёнка разойдётся по периметру тигля. При
необходимости сделайте задержку 3...5 секунд после разрыва оксидной
плёнки для выравнивания температуры по объёму тигля.
-
Температура нагрева опоки слишком мала,
или время её нагрева слишком короткое.
 Всегда
следуйте рекомендациям фирмы производителя используемой паковочной
массы по её применению. В зависимости от размера опоки, она должна
быть выдержана при конечной температуре примерно 30-50 мин для
того, чтобы гарантировать, что эта температура достигнет также
центра паковки.
Для
того, чтобы предупредить значительное понижение температуры опоки,
время между её извлечением из печи предварительного нагрева и
литьём должно быть как можно короче.
- Восковая композиция имеет объекты литья,
смоделированные слишком тонко.

Чем меньше толщина
стенок объекта литья, тем больше
поверхностное напряжение . Сплав не
может полностью заполнить литейную полость.
Не рекомендуется использовать толщину стенок объекта литья менее
0,3мм.
- Неправильно построена литниковая система.
 Правильно
сконструированная литниковая система должна обеспечивать быстрое
и ламинарное (плавное, однородным потоком) заполнение литейной
формы с необходимой скоростью, непрерывную подачу расплавленного
металла к затвердевающей отливке, выход газов из полости формы.
Объекты литья
должны охлаждаться в первую очередь и поэтому должны быть размещены
вне теплового центра опоки. Правильным считается их размещение
на минимальном расстоянии от боковой поверхности опоки и её дна.
На практике, обычно, необходимо выдерживать следующие расстояния:
4…5мм от боковой поверхности опоки и 4…5мм от её дна. Меньшие
величины этих размеров ограничиваются механической прочностью
материала опоки.
Литниковый
канал (каналы) и коллектор должны охлаждаться в последнюю очередь
и, следовательно, должны быть расположены максимально близко к
термическому центру опоки. В идеальном случае, коллектор должен
располагаться на середине высоты опоки, т.е. в зоне максимальной
температуры (тепловой центр). При этом коллектор обеспечивает
подпитку жидким расплавом объекты литья на стадии их кристаллизации,
препятствуя их неконтролируемой усадке.
- Повышенное содержание оксидов в
расплаве.

Используемые повторно литьевые конусы и
литники должны быть отпескоструены или протравлены кислотой. Количество
повторно используемого сплава не должно превышать указанного производителем
сплава (обычно не более30...50%). Если это не будет выполнено,
то накопление оксидов в сплаве может привести к снижению его жидкотекучести.
Это может привести к неполному заполнению полости объекта литья
расплавом, особенно, в тонких его частях.
- Недостаточный вакуум.
 Если
к моменту выполнения литья расплава в литейной камере вакуум не
достигает требуемых значений (–0,7…–0,8 кгс/см2), заполнение расплавом
литейной полости объектов литья будет затруднено. Оставшийся воздух
препятствует быстрому и равномерному движению струи расплава.
Постоянно контролируйте
работу пневмосистемы установки и, при необходимости, проводите
мероприятия по её техническому обслуживанию.
- Несвоевременная подача давления прессования
в плавильно-литейный блок.
 Несвоевременная
подача избыточного давления приводит к созданию условий для некачественного
литья.
Выбирайте время
литья "t1" таким образом, чтобы максимально синхронизировать
начало этапа прессования с моментом полного истечения расплава
из тигля.
Время нарастания
избыточного давления в плавильно-литейном блоке должно быть минимизированно.
Величина этого давления должна достигнуть 2 Бар за время около
2 секунд.
При необходимости,
проводите мероприятия по техническому обслуживанию пневмосистемы
установки.
2. Усадочная пористость объектов литья
Во время кристаллизации
сплава происходит уменьшение его в объеме. Если подача жидкого
расплава для того, чтобы компенсировать эту усадку, прерывается
или оказывается недостаточной, в объекте литья могут возникать
усадочные поры. Причин этого может быть несколько.
Неправильно сконструирована литниковая система.
 Объем
литниковых каналов, коллектора и прибылей должен быть больше чем
объем объектов литья для того, чтобы продолжать подпитывание последних
жидким расплавом во время процесса их кристаллизации.
Элементы, связывающие питающие части литниковой
системы с объектами литья должны присоединяться к самой толстой
части объектов литья.

Литниковые каналы, коллектор должны располагаться
максимально близко к тепловому центру опоки. Объекты литья должны
располагаться вне теплового центра опоки и приближены к боковой
стенке и дну опоки. В таком случае объекты литья смогут подпитываться
жидким расплавом из элементов литниковой системы (литниковый канал,
коллектор, прибыль), а охлаждение расплава в полости объекта литья
протекает быстро при сохранении однородных условий кристаллизации.
Низкая температура предварительно нагретой опоки.
Если температура предварительного нагрева опоки
слишком низкая или не выполнены условия выдержки опоки в течении
30...50 минут при максимальной температуре, центральная часть
опоки не успеет прогреться в достаточной степени. Тогда расплав
будет охлаждаться в питающих элементах (литниковые каналы, коллектор,
прибыль) раньше чем в объектах литья (особенно в массивных частях).
В этом случае сами объекты литья превращаются в питающие элементы
для остальных частей литниковой системы.
Слишком высокая температура предварительно нагретой
опоки.

При слишком высокой температуре предварительного
нагрева опоки охлаждение (и, соответственно, процесс кристаллизации)
расплава будет медленным. Существует риск, что питающие элементы
(литниковые каналы, коллектор, прибыль) и объекты литья будут
охлаждаться одновременно и в равной степени. Таким образом, условия
для направленной кристаллизации расплава не будут выдержаны.
Слишком высокая температура
расплава при литье.

Часто,
с целью повышения жидкотекучести расплава, осуществляют так называемый
"перегрев" металла. При этом необходимо помнить, что
с повышением температуры расплава существенно возрастает его способность
вступать в химическую реакцию с паковочной массой. Эта реакция
проходит с выделением газов, которые растворяются в расплаве.
При охлаждении расплава эти газы провоцируют возникновение так
называемой "газовой пористости".
Для исключения
причин появления газовой пористости не перегревайте металл. Фирмы
производители стоматологических сплавов допускают для различных
типов сплавов время задержки литья после разрыва оксидной плёнки
от 3 до 10 секунд. Читайте инструкции по применению используемого
Вами сплава.
Насыщенность расплавленного
металла газами.
 При
слишком ранней подаче избыточного давления (давление прессования)
в плавильно-литейный блок воздух вместе с расплавом попадёт в
литниковые каналы, произойдёт значительное газонасыщение расплава.
Газонасыщение расплава приведёт впоследствии к ярко выраженной
внутренней и поверхостной газовой пористости.
|
|
|
|
|
|
|
|
|
|
|
|
|
|
|
|
|
|
|
|
|
|
|
|
|
|
|
|
|
|
|
|
|
|
|
|
|
|
|
|
|
|
|
|
|
|
|
|
|
|
|
|
|
|
|
|
|
|
|
|
|
|
|
|
|
|
|
|
|
|
|
|
|
|
|
|
|
|
|
|
|
|
|